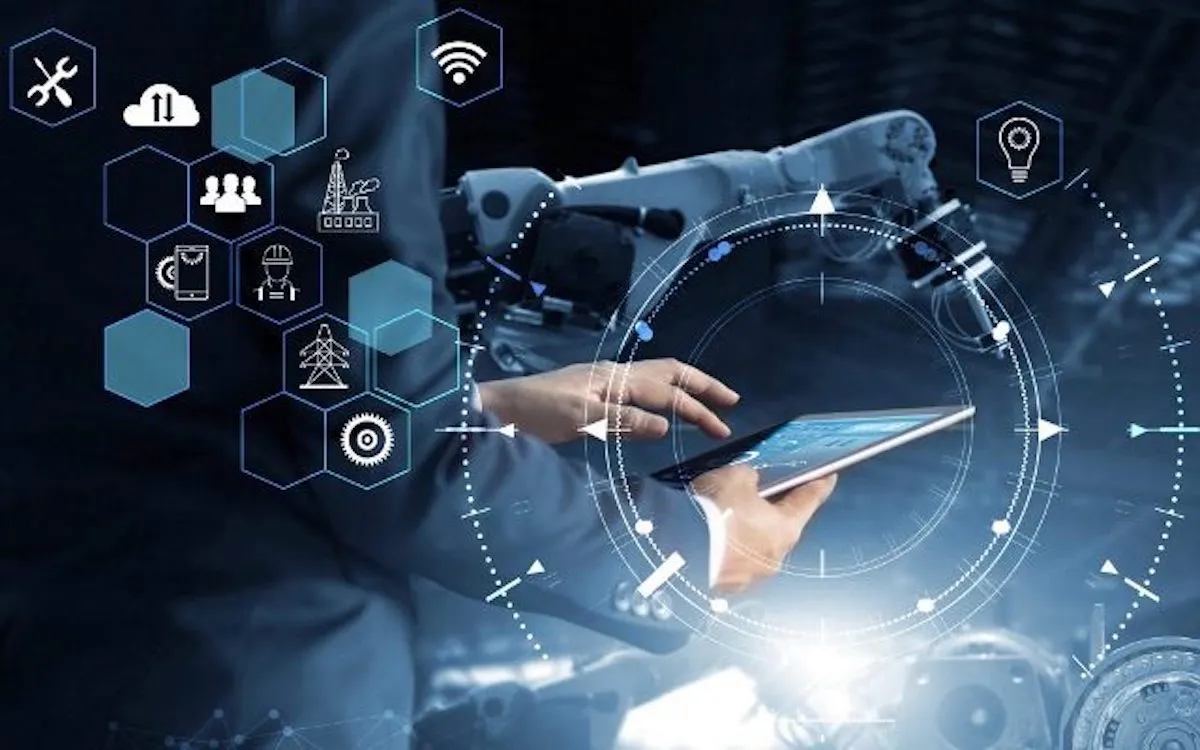
Page Visited: 606
Read Time:3 Minute, 7 Second
Crack Maintenance Engineer Interviews
Introduction:
When preparing for a maintenance engineer interview, it’s crucial to anticipate the questions you may encounter. This blog post aims to provide you with 12 common interview questions that maintenance engineers often face, along with expertly crafted answers. By familiarizing yourself with these questions and responses, you can boost your confidence and improve your chances of acing your next maintenance engineer interview.
- What is your experience with preventive maintenance?
Answer: Preventive maintenance is crucial in identifying and addressing potential issues before they become major problems. In my previous role, I successfully implemented preventive maintenance strategies, including regular inspections, lubrication schedules, and equipment calibration. - How do you prioritize maintenance tasks in a fast-paced environment?
Answer: Prioritization is essential in a fast-paced environment. I focus on critical equipment, safety-related issues, and production downtimes. By creating a priority matrix, I can allocate resources effectively and minimize disruptions. - Describe your approach to troubleshooting a complex machinery problem.
Answer: When troubleshooting complex machinery issues, I follow a systematic approach. I begin by gathering information, reviewing equipment manuals, and consulting with colleagues. Then, I break the problem down into smaller components and test each part until I identify the root cause. - How do you ensure compliance with safety regulations during maintenance activities?
Answer: Safety is my top priority during maintenance activities. I ensure compliance by adhering to relevant safety regulations, conducting regular safety trainings, implementing safety protocols, and providing personal protective equipment to the maintenance team. - Can you explain your experience with computerized maintenance management systems (CMMS)?
Answer: I have extensive experience with CMMS, including systems like SAP, Maximo, and eMaint. I have used these platforms to schedule and track maintenance activities, generate work orders, monitor inventory, and analyze equipment performance. - How do you handle unexpected equipment failures and minimize downtime?
Answer: In the event of unexpected equipment failures, I quickly mobilize the maintenance team, assess the problem, and identify the necessary resources. By maintaining a spare parts inventory and establishing relationships with reliable suppliers, I can minimize downtime and swiftly restore operations. - Describe your experience with predictive maintenance techniques.
Answer: I have experience implementing predictive maintenance techniques such as vibration analysis, thermography, and oil analysis. These methods help identify potential equipment failures before they occur, allowing for proactive maintenance actions. - How do you stay updated on the latest maintenance trends and technologies?
Answer: I am an avid learner and regularly attend industry conferences, workshops, and webinars. Additionally, I actively engage in online forums and subscribe to industry publications to stay abreast of the latest maintenance trends and technologies. - Can you discuss a challenging maintenance project you successfully completed?
Answer: In a previous role, I successfully led a major overhaul of a production line, replacing aging equipment and implementing automation. By coordinating with various departments, managing the project timeline, and ensuring effective communication, we completed the project on schedule and achieved significant productivity improvements. - How do you ensure effective communication between the maintenance team and other departments?
Answer: I believe in fostering open communication channels. Regular team meetings, clear documentation of maintenance activities, and feedback sessions are some of the methods I utilize to ensure effective communication between the maintenance team and other departments. - Describe your experience with root cause analysis (RCA) and its importance in maintenance.
Answer: Root cause analysis is vital in identifying the underlying factors contributing to equipment failures. I have experience conducting RCAs, utilizing techniques like the 5 Whys and fishbone diagrams. By understanding the root cause, I can implement effective corrective actions to prevent future occurrences. - How do you handle conflicting priorities from different departments?
Answer: Conflicting priorities are common in maintenance
Free Top 50 Electrical Interview Questions with Answers updated on 2023 Part 1.
I do not even know how I ended up here, but I thought this post was great. I do not know who you are but certainly you’re going to a famous blogger if you are not already 😉 Cheers!